Rethinking Gypsum Board Waste Management
Efficient waste processing is critical for industries dealing with large volumes of construction materials, and Gyproc S.p.A., part of the Saint-Gobain Group, faced this challenge on a major scale. With three production plants across Italy—Asti, Rimini, and Guglionesi—the company generates between 1,000 to 5,000 m³ of plaster board waste per month.
Traditional waste handling methods were proving inefficient and costly, prompting the company to look for a more sustainable and cost-effective solution to process plaster board waste directly on-site.
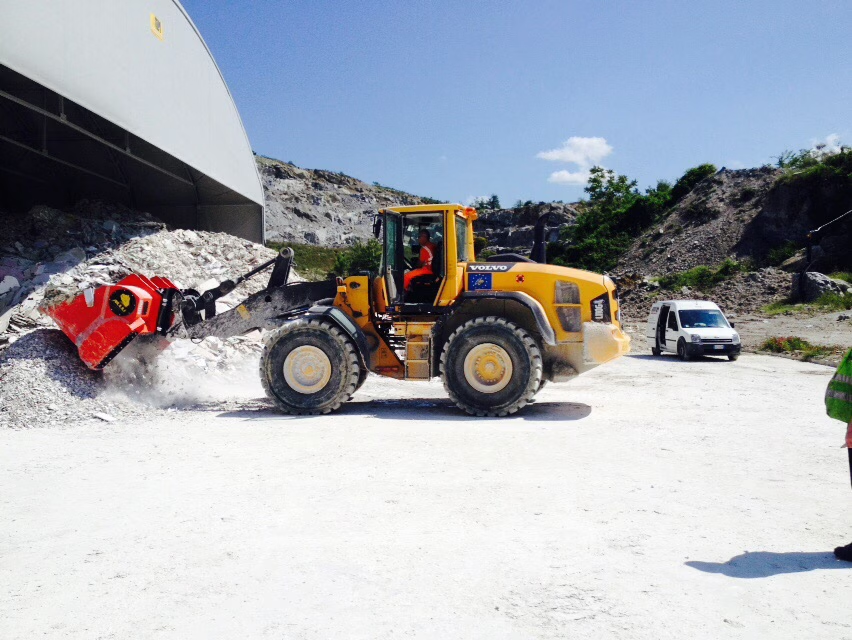
The Challenge: High Maintenance and Operating Costs of Traditional Crushing
At Gyproc’s Milan headquarters, the company relied on a REV crusher already available on-site. However, this approach came with several drawbacks:
- High maintenance and operating costs – The stationary crusher required frequent servicing, increasing overall expenses.
- Additional machinery required – A separate excavator was needed for loading, adding fuel and labor costs.
- Limited flexibility – The fixed crushing system meant additional handling time and transport logistics.
With increasing waste volumes, Gyproc needed a solution that was mobile, efficient, and cost-effective, without compromising processing quality.
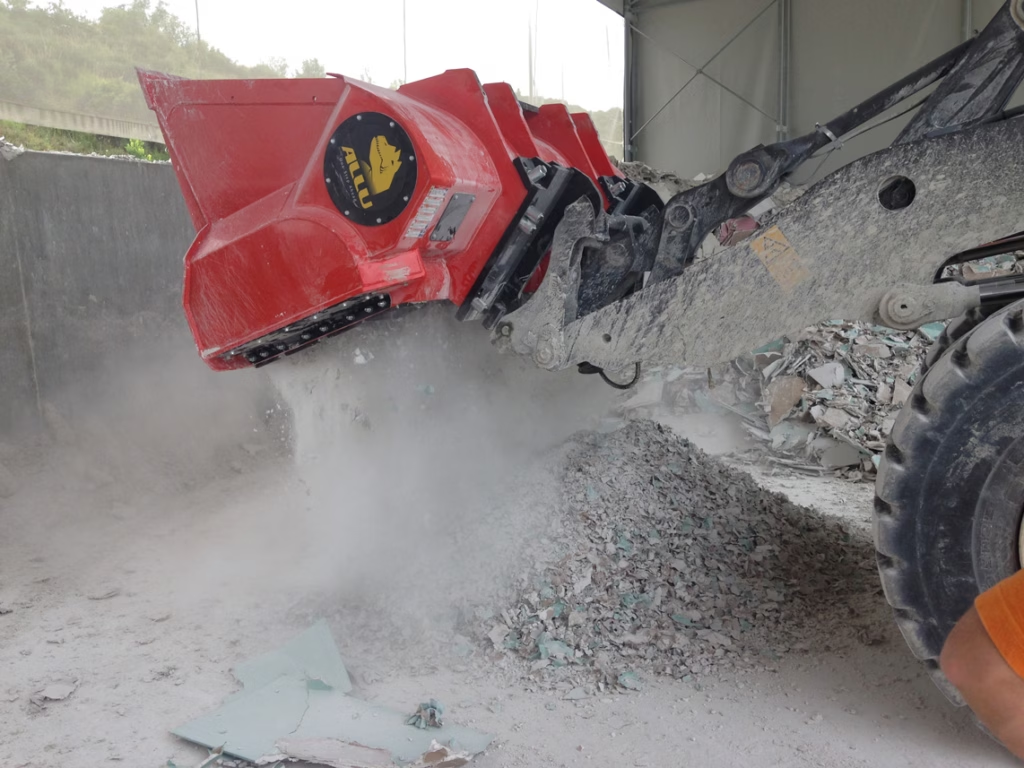
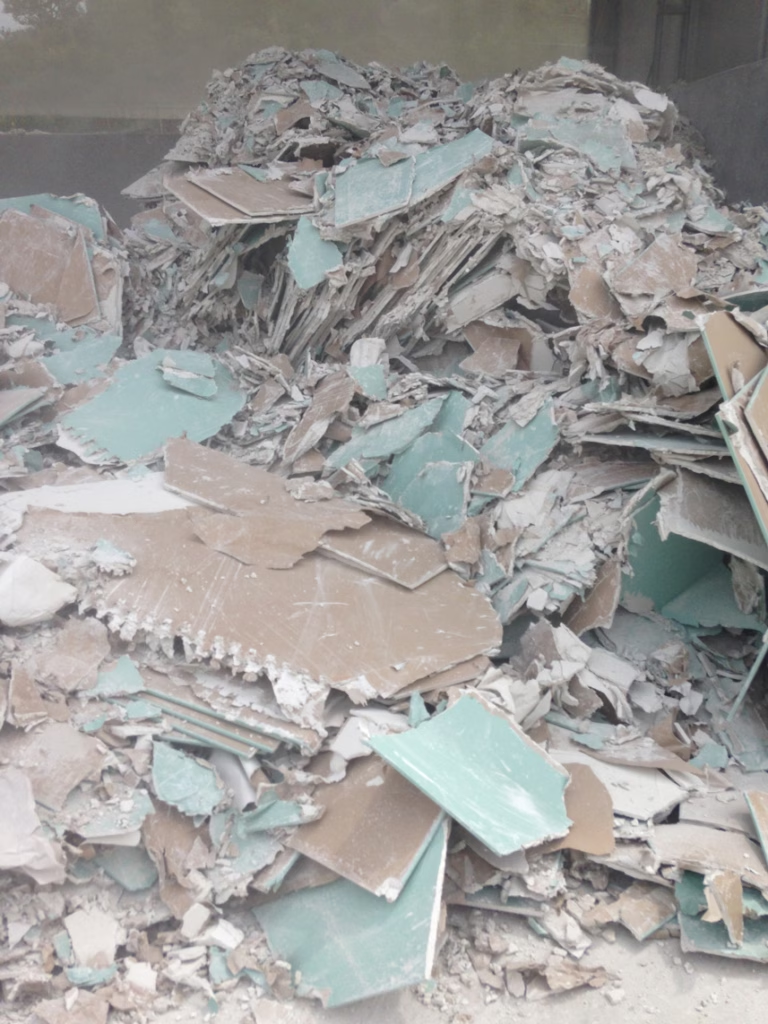
The Solution: ALLU Transformer D-Series – A Mobile, One-Step Approach
To replace the high-maintenance stationary crusher, Gyproc introduced the ALLU Transformer D-Series, specifically the DS 3-23 / XHD 40 equipped with long hammers on the center drum, mounted on their Volvo L110G wheel loader.
This upgrade enabled crushing, screening, and refining of plaster board waste in a single operation, eliminating the need for a separate crushing unit. With the ALLU D-Series, Gyproc:
- Reduced equipment needs – The wheel loader handled both processing and loading, eliminating the need for an additional excavator.
- Lowered operational costs – Fewer machines running meant significant savings on fuel, labor, and maintenance.
- Increased efficiency – Waste was processed directly on-site, reducing handling time and transport needs.

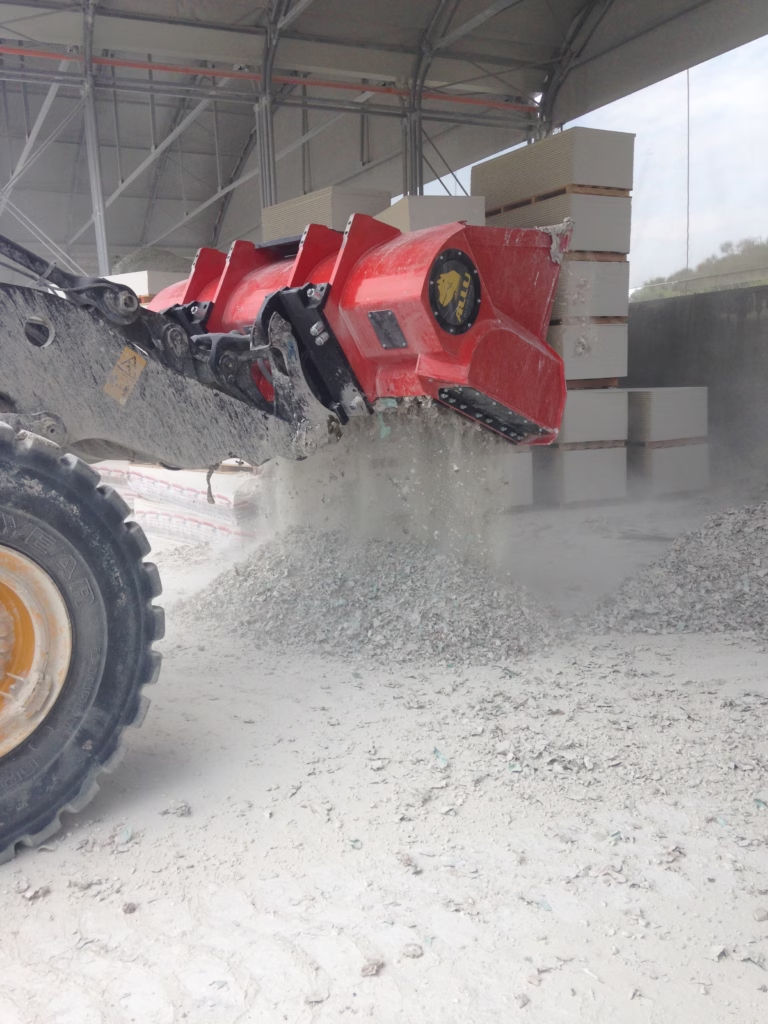
The Results: Faster Processing, Cost Savings, and a Quick ROI
To validate the efficiency of the ALLU D-Series, Gyproc conducted a two-day trial, testing both capacity and final product quality. The results demonstrated clear benefits:
The company previously spent €16,000 per month on the REV crusher, including maintenance and additional operating costs. The ALLU Transformer purchase cost was recovered in approximately six months, making it a highly cost-effective solution. Additionally, with the wheel loader now handling both processing and loading, Gyproc no longer needed an extra excavator, further streamlining operations.
This more efficient and mobile approach helped Gyproc improve material recovery, reduce costs, and simplify its waste processing workflow.
Expanding the Success Across Italy
Following the success of the ALLU D-Series screening bucket, similar setups were adopted by multiple companies across Italy, including:
- Gessi del Lago d’Iseo (GR) – DS 3-23 / 40 XHD
- Knauf Interni (PI) – DN 3-17 / X75
- Biondi Srl (PG) – SC 3-15 / 35 XHD
- Lafarge Gessi Spa (AQ) – DS 3-23 / 40 XHD
- Gyproc (Saint-Gobain Group, Milan) – DS 3-23 / 40 XHD
The introduction of the ALLU Transformer D-Series at Gyproc’s Milan plant set a new benchmark in waste management, proving that mobile, on-site processing can replace high-maintenance crushers while delivering significant cost savings.
Looking Ahead: Smarter Waste Processing for a More Efficient Future
With the success of the ALLU D-Series, Gyproc has demonstrated that on-site waste processing is more efficient, cost-effective, and sustainable. By investing in mobile screening technology, they have optimized their production workflow, reduced their environmental footprint, and set a new standard for smarter material handling in the gypsum industry.
➡ Looking for a more efficient way to process construction waste? Discover how ALLU can transform your operations.