In the small town of Pukavik in southern Sweden, Elleholms Maskin AB runs a tight ship. With nearly 80 employees and a heavy-duty fleet of over 30 excavators, 20 trucks, and a full suite of loaders and screeners, the company is one of the most active regional contractors in the area. Founded by Johannes Henriksson, the company has grown steadily by staying hands-on and taking on the work others passed up.
That mindset of staying hands-on and making things work is what led to their latest improvement at the recycling yard. The site handles everything the region’s construction sites throw at it: excavated soil, concrete rubble, stumps, tangled roots, and shredded wood. One truckload at a time, it adds up especially the incoming waste material, which used to grow into towering stockpiles before it could even be processed.
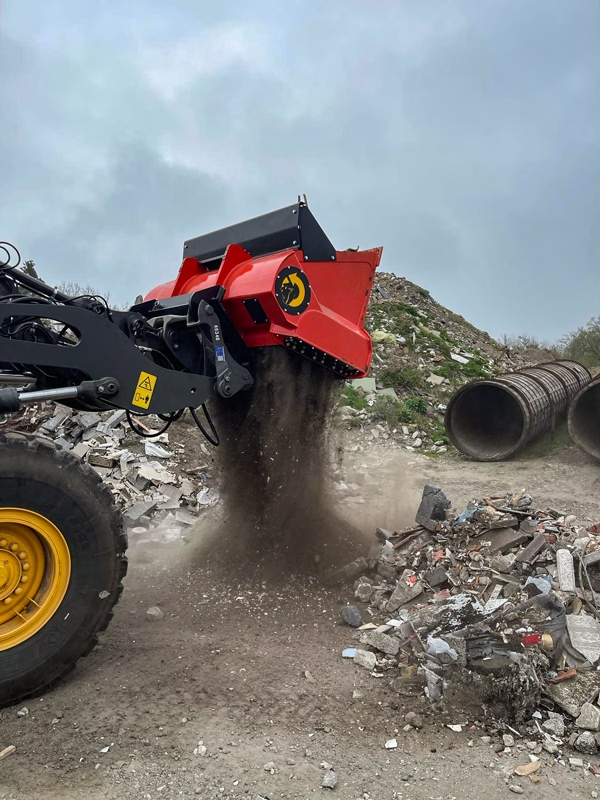

Challenge
For years, the company’s screener at the Elleholms yard was responsible for both clean soil and recycled waste material. But it couldn’t be in two places at once.
“We used to let the waste pile up until we had no choice but to deal with it,” the crew explains. “Sometimes it hit 10,000 cubic meters before we could even start sorting.”
This bottleneck took up valuable space on-site and tied up resources. On top of that, it interrupted the flow of higher-priority work like soil and gravel production. The problem wasn’t the volume — it was the timing. The incoming waste needed to be screened earlier, not later.
Solution
The team brought in an ALLU DN 3-17 screening bucket with TS08/16 drums. It’s now used to screen waste material immediately on arrival, without waiting for the main screener. Positioned right where the trucks unload, the bucket separates material at the source — freeing up space, simplifying logistics, and keeping the rest of the operation on track.
“We don’t have that massive pile anymore,” they say. “It’s under control now. And our main screener is always available for what it’s really meant to do — soil and gravel.”
The bucket also takes on the dirtier jobs like bark and tree stumps mixed with topsoil that aren’t ideal for fixed setups. It can even be taken to job sites, mounted on an excavator, to screen material directly on location.
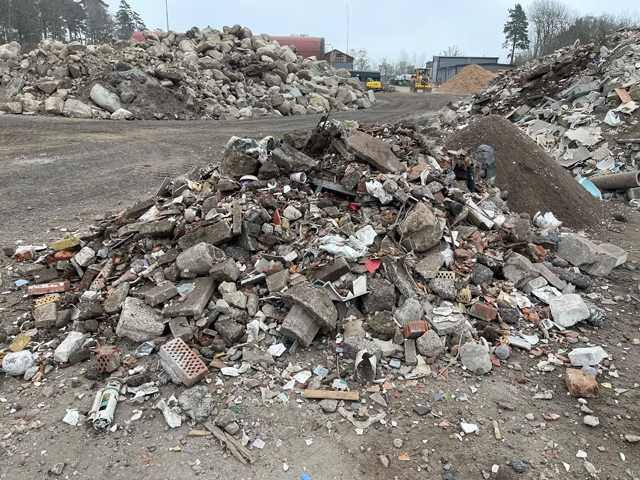
Operational Use
The ALLU DN 3-17 is now a regular part of the workflow at Elleholms Maskin’s recycling yard. Instead of transporting material twice or delaying processing, the crew uses the bucket to break down and sort loads on the spot. It’s also used for small, irregular piles that aren’t worth starting up the entire plant for.
And the setup is flexible when needed, the bucket heads to jobsites and handles screening directly at the jobsite.
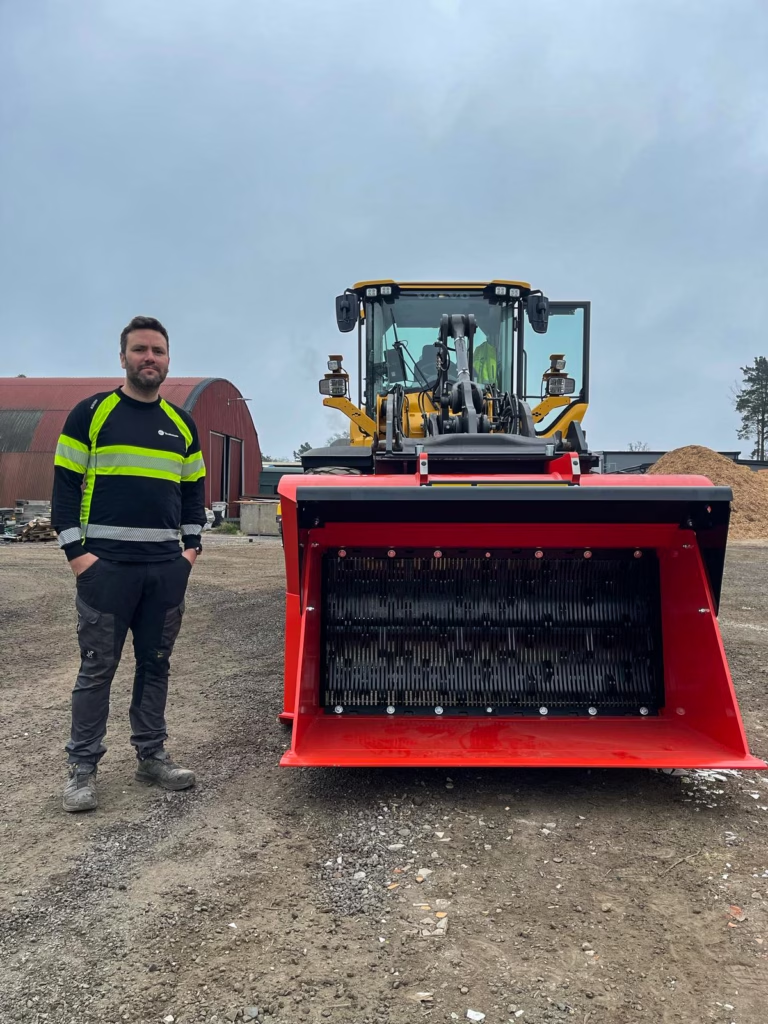
Benefits
Henriksson’s approach has always been simple: make room for people, make room for work, and don’t waste time on waste. The new setup with the ALLU bucket is just an extension of that mindset — efficient, adaptable, and built around real-life needs. What used to be a growing problem is now a solved one. The yard runs cleaner, leaner, and with fewer interruptions.
• Material is screened immediately upon arrival
• Waste piles remain small and manageable
• Fixed screener can focus on high-quality soil and gravel
• Mixed material—like soil with bark or tree roots—is processed with ease
• Bucket can be used at job sites, not just in the yard
• Reduces double handling, saves time and space
The investment wasn’t about technology, it was about keeping the operation moving. That’s how Elleholms Maskin works: steady, thoughtful, and always a few steps ahead of the next pile.
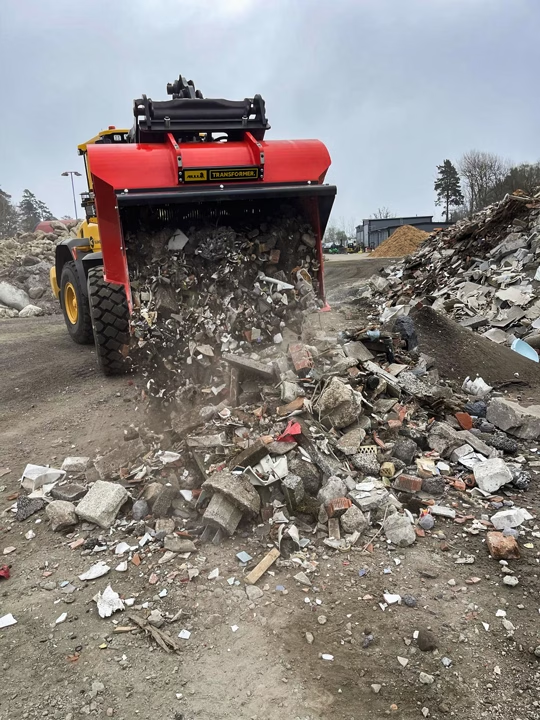